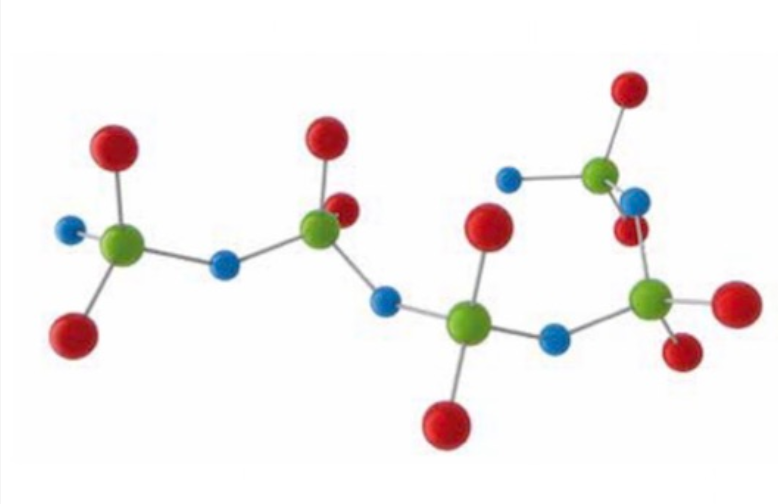
Molecular Structure & Resulting Properties
In contrast to other polymeric insulation materials, silicones (also known as polydimethylsiloxanes) are not made up of a carbon to carbon backbone. Rather, they consist of repeating silicon-oxygen (siloxane) groups with two methyl groups each bonded to the silicon. As such, they differ widely from hydrocarbon-based materials. One accepted standard abbreviation for silicones is VMQ, where Q stands for rubber having silicon and oxygen in the polymer chain while M indicates that the material mainly contains methyl groups (CH3). V stands for the vinyl groups (R-CH=CH2) that represent the material’s curable species. It is this chemical structure that makes silicones able to satisfy important properties required across diverse power industry applications.
Ball-model of polydimethylsiloxane (PDMS). Green represents silicon atoms, blue is oxygen atoms.
Stability Under UV Radiation
Silicones have a structure similar to organically modified quartz. The high bonding energy of the silicon to oxygen (Si-O) backbone provides stability against breakdown by UV irradiation. For example, the bonding energy of Si-O bonds is 444 kJ/mol versus only 348 kJ/mol for C-C bonds. Shortwave sunlight at 300 nm has an energy content of about 6.2×10-22 kJ (i.e. 398 kJ/mol) and can therefore cleave C-C bonds but not the Si-O bond that remains stable. Even high UV and harsh weather conditions such as found in coastal regions or deserts have little impact on this resistance property. Silicones show only slight changes in mechanical and wetting behavior, even after extended accelerated weathering testing in climatic chambers.
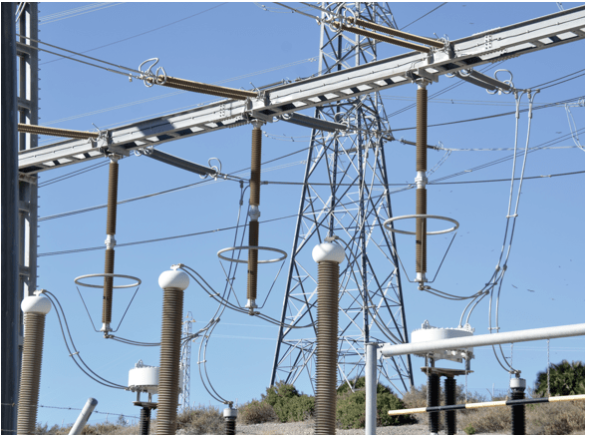
Performance under persistent high UV is key to successful application of
silicone-housed insulators, arresters and bushings, such as here in southern Spain.
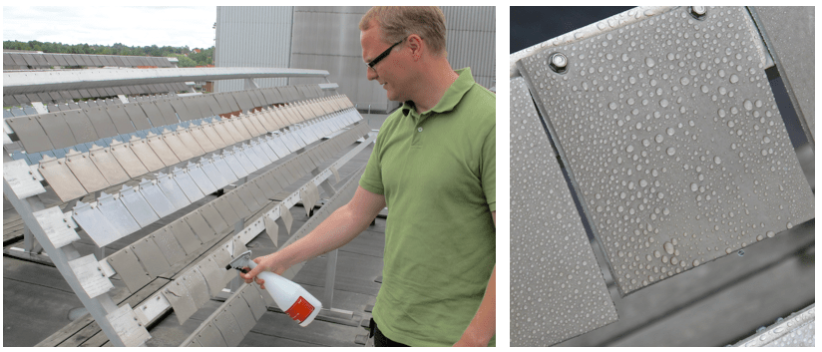
Testing hydrophobicity of silicone materials after exposure to climatic stresses.
Hydrophobicity
Silicone polymers and molded components made with silicone elastomers exhibit low surface energy that does not allow water to spread out over their surface, i.e. a hydrophobic or water repellancy property. This highly desirable characteristics can be evaluated by measuring wetting angle of water droplets on the surface of silicone specimens.
Inherent water repellency of silicone elastomers is key to superior pollution performance.
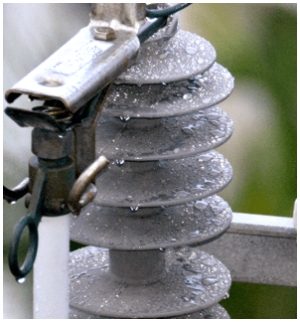
Wetting behavior of silicone cutout.
Service experience confirms that leakage current along an electrically stressed hydrophobic surface is limited to low values. Wetting performance of insulation therefore increases compared to the same surface covered with a layer of film, as long as the droplet layer of water remains mostly intact. This same characteristic also extends to polluted surfaces as a result of the hydrophobicity transfer effect. Silicone elastomer formulations contain a tiny but not negligible amount of short-chain, low molecular weight (LMW) siloxane chains. When driven by a difference in concentration between the base silicone elastomer and the pollution layer, these mobile species migrate into and encapsulate the pollution layer. In fact, the rough surface of the now hydrophobic pollution layer often shows an even higher wetting angle than the shiny surface of the clean silicone. This effect promotes sustained hydrophobicity.
Water droplet on clean silicone coating (left) and on coating with pollution layer (right) due to hydrophobicity transfer effect.
Thermal Stability
Due to chemical structure, silicones demonstrate stability even at elevated temperatures. Most silicone elastomers remain stable and elastic up to 200°C while modified products can withstand as high as 300°C. This is confirmed by tests of weight loss of different silicone elastomers (VMQ A, B and C) stored at 200°C. It is important to note, however, that thermal stability is not itself a physical property but rather requires definition of permitted changes in key performance properties, such as elongation at break, hardness, weight loss, etc., within the time period considered. For example, it has been shown that the tensile strength of a silicone elastomer exposed to 200°C in air retained 80% of its initial value even after 700h constant exposure. Standard silicone elastomers (VMQ) maintain elasticity at temperatures down to -45°C, which makes them suitable for use in cold temperatures as well. In fact, special modified silicone gels remain flexible up to -100°C.
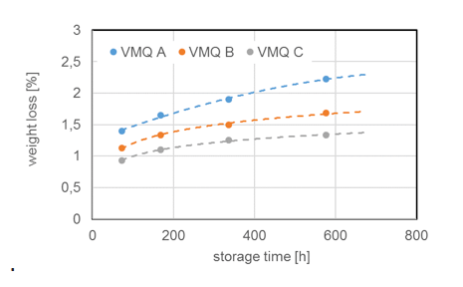
Weight loss of three different standard silicone elastomers (VMQ) during storage at 200°C.
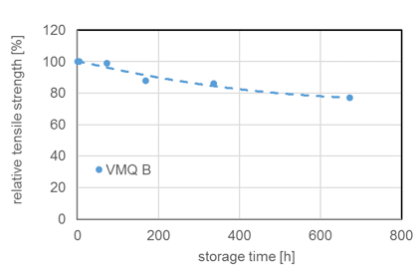
Tensile strength of silicone elastomer versus storage time at 200°C.
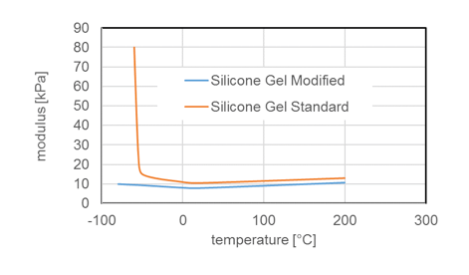
Modulus of standard silicone gel and modified silicone gel exposed to high and low temperatures.
Flame Retardancy
Silicones ignite only at very high temperature and thus exhibit good flame-retardancy. Typically, silicone elastomers show either class V0 or HB under the relevant test criteria, making them particularly safe in operation. Moreover, if they do ignite, they burn without producing toxic gases so they are well suited for applications subject to strict fire safety requirements, e.g. subways, tunnels, high-rise buildings, etc.
Key Properties for Electrical Applications
Silicones offer attractive properties for electrical applications in general but each specific application may require a somewhat different key property. For example, the original focus for insulator coatings was on water-repellancy of the RTV silicone material. Later, when composite insulators were introduced, the high UV resistance of silicone elastomers offered another advantage. Such key performance properties for various applications have remained largely the same over the years, with the possible exception of transformer fluids where the focus has shifted from low flammability to temperature resistance.
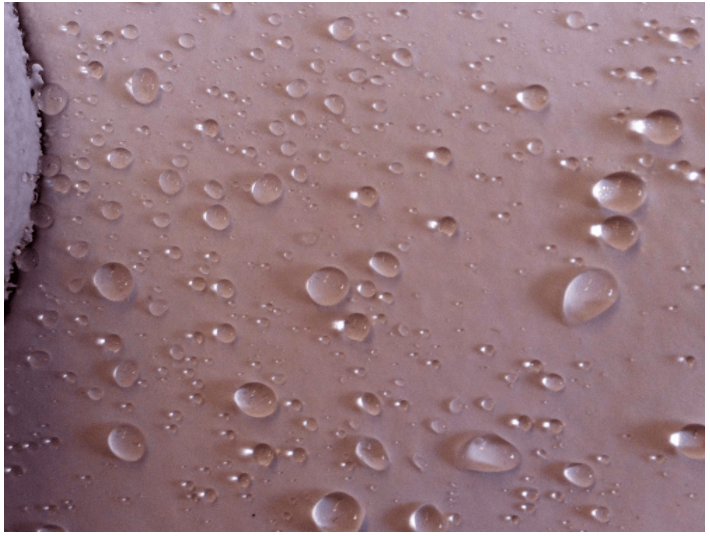
Hydrophobicity of glass insulator with RTV silicone coating.
Key (green) and other advantageous properties per application.
Product Groups
Silicone Elastomers
Silicone elastomers are the most important group of silicones serving the world’s transmission and distribution industry. Owing to the wide range of potential applications, they differ with respect to viscosity and curing systems and are continually undergoing further refinement to optimize production and performance. There are three major groups of these elastomers.
HCR logs used in molding insulators and core rods.
Drums of LSR two component materials supply insulator molding machine.
High Consistency Silicone Rubber (HCR)
These materials, with high viscosity and typically supplied as logs are used for injection molding, press molding or extrusion. HCRs are typically peroxide curing materials but one and two-component addition curing systems are also available.
Liquid Silicone Rubber (LSR)
These 2-component materials have viscosity of some 10,000 to 1,000,000 mPa and are supplied in drums or similar. They are either injection molded or directly filled into a mold using meter-mixing devices (low pressure mold filling or LPMF). All LSRs are addition-curing materials.
RTV Silicones
Silicones that often have low viscosity and whose formula allows cross-linking at comparatively low temperature are grouped under Room Temperature Curing materials (RTV). While the ‘V’ stands for vulcanization, crosslinking of these materials occurs either by polyaddition or polycondensation. RTV materials can be 2-component (rubbers) or 1-component (e.g. coatings).
Silicone Gels
Silicone gels are insulating materials that have the potential to replace liquids or elastomers, depending on application. They pose less risk of leakage than fluids yet perfectly fill hollow spaces, even of complex shape. These gels, typically used as insulating compounds for cable accessories, etc., are pourable, addition curing, two-component silicones that cure to soft, gel-like products. The unmixed components usually demonstrate low viscosity with excellent pouring properties. The cured silicone gel generally adheres well to all substrates in contact with it.
Silicone Fluids & Pastes
Silicone fluids have proven themselves as coolants and insulating materials in modern transformers due to outstanding temperature resistance. A further important application is in the area of high voltage cable accessories. Silicone fluids are non-reactive, linear PDMS with chain length from 2 to well over 1000 Si atoms. Adding thickeners makes it possible to produce silicone pastes, used for example as lubricants in the electrical industry.
Curable Silicone Compounds
The primary components in curable silicone compounds are polysiloxanes, produced by converting quartz into silicon metal using a metallurgical process followed by transformation into chlorosilanes based on the Müller-Rochow process. Silanes are then converted into polysiloxanes by hydrolysis technology. The properties of polysiloxanes and the products made from them depend greatly on structure of their chemical backbone and attached functional groups. Apartfrom these polysiloxanes, silicone compounds often contain reinforcing fillers, cross-linkers and additives to achieve desired processing and product performance. Conversion of the uncured compound into an elastic state – known as curing or cross-linking – involves formation of covalent bonds between polymer chains. Depending on class of silicone rubber, peroxides, silanes or SiH-containing siloxanes are required for such cross-linking to occur.
Fillers reinforce the elastic silicone network and help adjust rheological properties. The nature, composition and quantity of these fillers are critical in determining the properties of the uncured and cured rubber. For example, the most effective reinforcing filler is pyrogenic silica (fumed silica) with high BET surface. Additional fillers such as quartz, alumina trihydrate (ATH) and carbon black might also be used to achieve the desired thermal stability, media resistance or electrical properties.
The suitability of a compound for a particular processing method is dictated by its rheological properties, i.e. viscosity, which describes its flow characteristics. Higher viscosity means less pourable. Viscosity of Newtonian fluids such as polysiloxanes is independent from shearing. By contrast, compounds made from polysiloxanes and fillers show non-Newtonian behavior, whereby there is significant decrease in viscosity with increased shearing. Rheological behavior of uncured silicone rubber is important since it facilitates manufacture of electrical components by extrusion or injection molding. The significant shear-thinning effect as well as solubility of air must also be taken into account when processing silicone rubber. Settings such as temperature, pressure and flow control in state-of-the-art molding equipment enable reliable production of large volume pieces e.g. cable accessories as well as articles having complex geometry and high precision
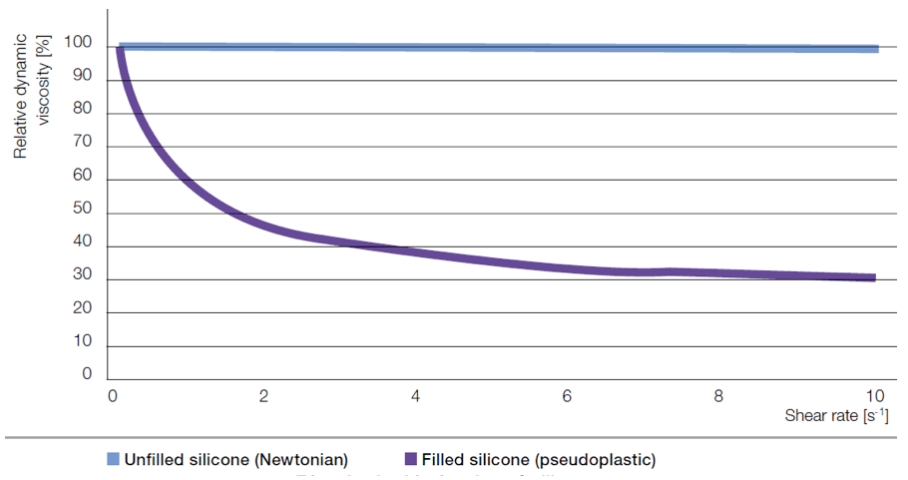
Rheological behavior of silicones.
Various technologies exist to cross-link polymers such as silicone elastomers with three having achieved broad commercial application:
1. Condensation-Curing Silicones
Condensation-curing silicone rubbers for electrical applications come as ready-to-use one-component compounds. Cross-linking technology here is based on reaction between Si-OH groups and/or hydrolysable Si-X groups in the presence of moisture. Right after application, the material starts to cross-link when in contact with the moisture in air. Depending on nature of the cross-linker, small amounts of acetic acid, amine or neutral by-products such as alcohol are released during curing.
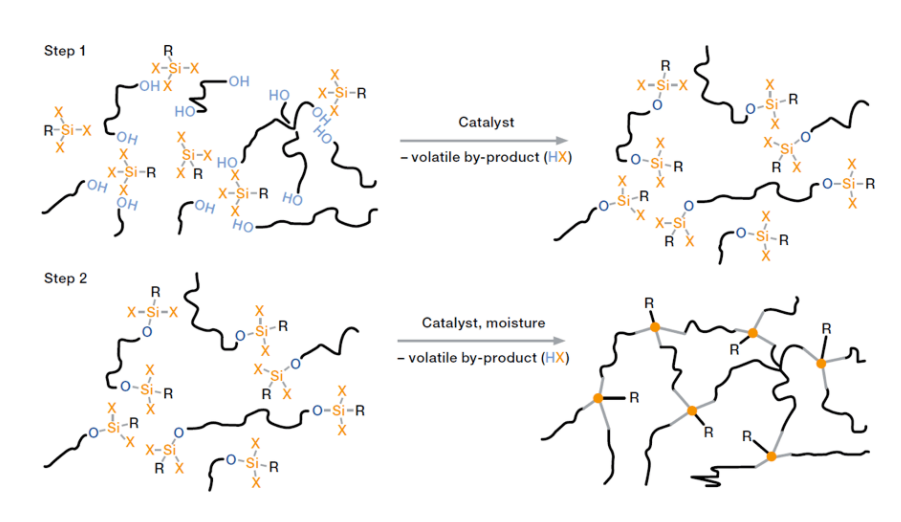
Cross-linking using condensation curing.
Cross-linking starts with formation of a skin on the rubber surface and gradually progresses into the compound itself. Curing rate of these silicones is limited by speed of diffusion of moisture into the compound. Therefore, monitoring and controlling temperature and relative humidity is recommended to ensure reliable curing. Since they are ready-to-use systems not sensitive to inhibition by other substances, condensation-curing silicone rubbers exhibit easy handling and processing properties. Because of good adhesion to a variety of substrates, such as metallic parts, ceramics, plastics and cured silicone rubber, such silicones are ideal for sealing, bonding and coating. High diffusion rate of moisture through thin layers of silicone rubber as well as ease of handling and excellent adhesion have led to development of silicone coatings for glass and ceramic insulators as well as other components. But in the case of short cycle time, production of large volume pieces and also for heat and media resistance properties, applicability of condensation-curing RTV-1 technology is limited and other cross-linking systems are preferable.
2. Peroxide Induced Cross-Linking
Peroxide curing involves organic peroxides. At elevated temperatures, these decompose to form highly reactive radicals that chemically cross-link the polymer chains and lead to highly elastic, three-dimensional networks. For example, peroxide-induced curing is used to produce commerical compounds such as so-called ‘high consistency rubber’ that contain polymers with high molecular weight and relatively long polymeric chains.
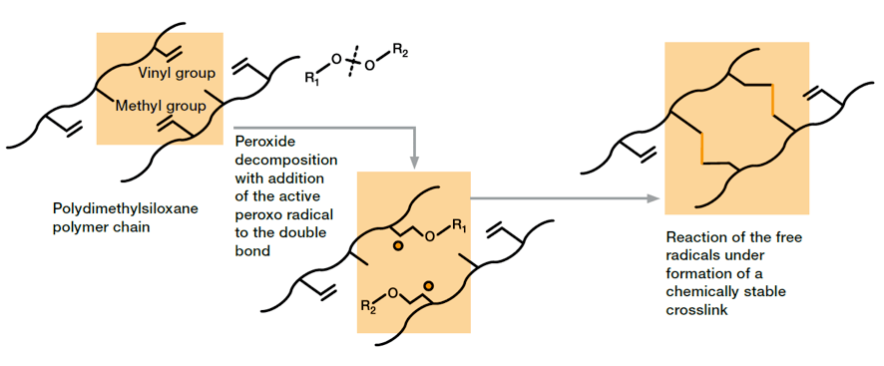
Peroxide-induced curing of silicone rubber.
Several peroxides have proven suitable for cross-linking silicone rubber. Apart from temperature range of cross-linking, which is characteristic for each and typically ranges from 100 to 200°C, radicals formed during vulcanization differ in regard to tolerance to atmospheric oxygen. Suppliers of silicone rubber have several peroxide systems in their portfolios, allowing them to provide material solutions for common processing methods such as extrusion, press and injection molding. Some applications mazy require additional post-curing of the peroxide- cured silicone rubber to improve mechanical properties (e.g. low compression set) or to remove volatile cleavage products. This technology has been widely applied for decades due to excellent mechanical strength of the products being made, better resistance to inhibitors or contaminants versus platinum-curing and proven, technically-mature processes.
3. Platinum Catalyzed Hydrosilylation (Addition Curing)
Platinum-catalyzed addition curing, also known as hydrosilylation, is a reaction between Si-H rich cross-linkers and vinyl- functionalized polysiloxanes. Addition curing is applicable to both solid and liquid silicone rubber and the reaction starts even at low temperatures once the catalyst is mixed with other components. Adding inhibitors allows pot life to be adjusted to hours, days and even months in the case of one-component ready-to-use systems. Addition curing enables cross-linking at room temperature as well as temperature-induced heat curing systems.
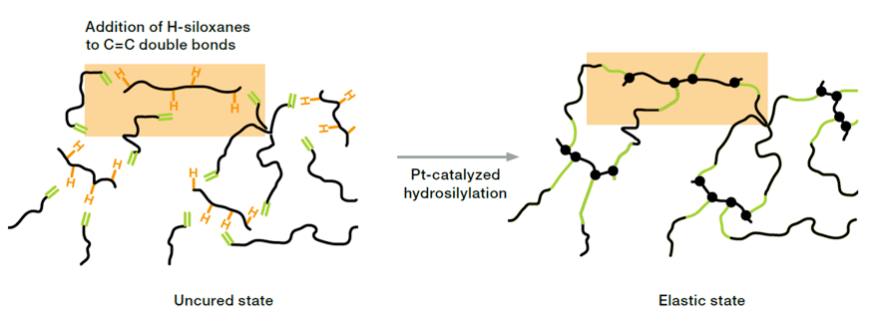
Platinum-catalyzed curing of silicone rubber.
The outstanding activity of platinum enables catalyst loading down to the ppm range. For fabricators that apply addition curing products, it is therefore important to be aware that even traces of platinum can trigger cross-linking reactions (known as platinum contamination). Due to such low platinum content, even tiny amounts of ‘poisons’ can inhibit the catalyst, especially amine and sulfur containing compounds. Separation of production lines, e.g. from those using organic rubber, as well as thorough cleaning of equipment is vital to prevent cross contamination. Despite the above behavior of Pt-curing compounds, application of addition curing is stateof- the-art since this technology offers advantages in regard to manufacturing and product properties.
Raising temperature significantly increases rate of cross-linking relative to peroxide curing systems. A well-adjusted balance and concentration of Pt-catalyst and inhibitors, along with correct settings of manufacturing equipment, allow shorter cycle time and more energy efficient production of even large volume items. Good de-molding properties and the dry surface of cured rubber pieces further help optimize the manufacturing process. Addition curing facilitates homogeneous, well-defined silicone rubber networks with outstanding tear strength and elasticity, whereas selectively loose cross-linking of polysiloxane-chains enables formation of ‘non-bleed’ silicone gels with exceptional sealing properties. Unlike peroxide curing, platinum catalyzed cross-linking does not liberate volatile by-products, which is another major advantage for certain applications.
Challenging and versatile demands placed on components in the power sector require a portfolio of different materials and technologies for silicone elastomers. Polymeric structure and functionality, volume and nature of filler as well as cross-linking density and applied curing method all help give silicone elastomers outstanding properties. But deep understanding of all possible interactions between ingredients is essential to achieve stability during storage, reliable processability and product performance that is best suited to the needs of the application.
Applications
Insulators & Surge Arresters
Silicone elastomers are used to manufacture composite long rod and hollow core insulators as well as a variety of surge arresters of different design. These are intended for applications from 10 to 1000 kV as suspension, tension, post and railway insulators, among others. Hollow-core insulators are used to manufacture arresters, bushings, instrument transformers and other electrical apparatus. Modern production processes permit diameters of one meter and more and lengths of over 10 m.
Silicone Coatings for Insulators
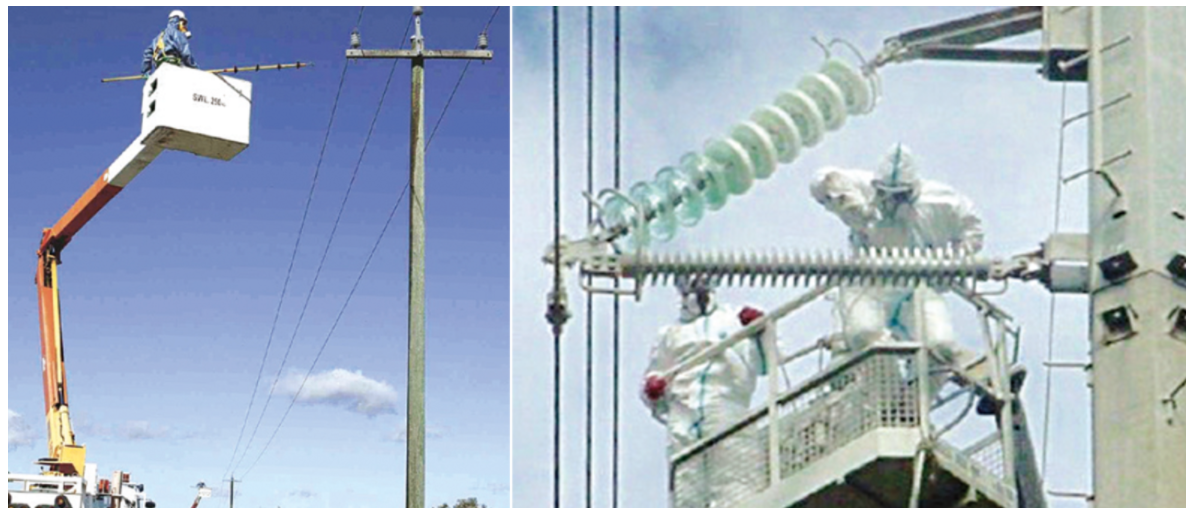
Applying RTV silicone to coat line insulators.

Coated bushings on transformer at seacoast.
Silicone coatings are applied to glass or porcelain insulators exposed to contamination and wetting conditions to mitigate risk of pollution flashover and pole fires. Coatings can then be re-applied, when needed, making them a cost-effective, long-term alternative to replacing affected components. Silicone coatings can even improve the electrical properties of aged epoxy resin insulators and equipment. Manufacturers of porcelain and glass insulators now promote application of silicone coatings early on in the supply chain to make their products water repellent. Silicone coatings are usually 1-component, room-temperature curing silicone systems that cure under the influence of moisture from the surrounding air. Materials are thoroughly stirred, decanted into the processing machine and sprayed onto the insulating part
Cable Accessories
Cable accessories, used outdoors, indoors and underground, must offer outstanding insulation properties. Moreover, mounting techniques such as slip-on- and cold-shrink benefit from highly elastic materials. Cable joints and terminations are now used from 10 kV to 500 kV and can perform more reliably due to silicone rubber’s hydrophobic property and resistance to elevated temperature, UV and ozone. A special requirement for cable accessories is grading inner electrical field. Special types of conductive materials and those having increased dielectric permittivity are used for this purpose. Electrically conductive coatings are also available for screening applications in cable joints
Production Technologies
Injection Molding
Injection molding is the most common and also most efficient method to process large quantities of silicone elastomers due to consistently short cycle time and high productivity. Suitably configured machinery and tools permit flexible production and low material losses. This process is applied for both HCR and LSR to achieve desired characteristics of being suitable for large numbers of small to medium-sized pieces with high dimensional accuracy.
Low-Pressure Mold Filling
Low-pressure mold filling, or casting, is suitable for large volumes of silicone such as in high voltage cable joints or hollow core insulators. A low viscosity silicone rubber with good flow properties is generally used to guarantee high volumetric flow rate and reliable production. Characteristics of this process are cost-efficiency for large-volume parts and medium capital outlay.