1 Introduction
Room temperature vulcanized liquid silicone rubber can be cross-linked and vulcanized naturally at ambient temperature. Its application process is simple and convenient, which provides users with a lot of convenience and is widely used in many fields. Among the major varieties of silicone products, liquid silicone rubber is the category with the fastest growth in production and sales and technological progress.
Taking two-component condensation reaction vulcanized liquid silicone rubber as an example, the general production process of silicone rubber compound and vulcanizing agent is as follows:
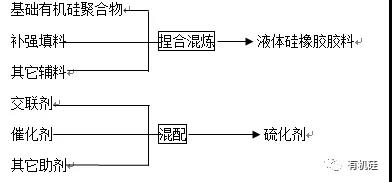
Practitioners in the production and application of liquid silicone rubber are well aware that the viscosity of liquid silicone rubber and the mechanical strength of its vulcaniz It is hoped that the liquid silicone rubber compound has good fluidity, that is, the viscosity of the rubber compound is appropriately low; and in many applications, the vulcanized silicone rubber is required to have appropriately high mechanical strength. The mechanical strength of liquid silicone rubber vulcanized rubber is closely related to the viscosity of its rubber compound. The general rule between the two is: if the vulcanized silicone rubber is required to achieve higher mechanical strength, the proportion of reinforcing fillers is often larger. The viscosity of the silicone rubber compound should increase accordingly; on the contrary, if the silicone rubber compound is required to have good fluidity, the proportion of the filler should not be too large, and the mechanical strength of the vulcanized rubber of the low-filled liquid silicone rubber compound is relatively reduced.
In order to improve the overall performance of liquid silicone rubber, the author has done some research experiments. This article briefly describes the common methods of condensation reaction vulcanization type liquid silicone rubber and addition reaction vulcanization type liquid silicone rubber, and briefly describes the general methods for reducing the viscosity of silicone rubber and improving the mechanical properties of vulcanizates, focusing on the summary and introduction of reducing the viscosity of the rubber and increasing the vulcanizate. Comprehensive technical measures of intensity. 2. General methods to improve the mechanical properties of liquid silicone rubber vulcanizates
2.1 Liquid silicone rubber base polymer The mechanical strength of silicone rubber is related to the molar mass of the base polymer. It is known that crosslinked products with low molar masses have low strength, so polysiloxanes with a molar mass of 4×104 g/mol (corresponding to a viscosity of 3×103 mPa·s) or more are usually used as the basic polymerization of liquid silicone rubber. Things. In practical applications, due to fluidity requirements, the viscosity of the silicone polymer used for liquid silicone rubber should generally not exceed 100×103 mPa·s (corresponding to the molar mass of the polymer about 14×104 g/mol).
2.2 The molecular chain of polydimethylsiloxane, the base polymer of reinforcing filler silicone rubber, is very flexible, and the molecular chain entanglement is weak. Therefore, the tensile strength of vulcanized silicone rubber without reinforcing filler is only 0.3 to 0.4 MPa. Such low strength lacks practical value in many occasions. The liquid silicone rubber in practical application must add reinforcing fillers to the basic silicone polymer, and through kneading and mixing, to promote the filler and the basic polymer to fully infiltrate, in order to maximize the reinforcing effect. Silica is the most suitable reinforcing filler for silicone rubber. Adding vapor-phase white carbon black or precipitation white carbon black to the silicone polymer can improve the mechanical strength of vulcanized silicone rubber. As far as commercial white carbon black is concerned, most of the reinforcing effect of gas phase method white carbon black is better than that of precipitation method white carbon black, but the thickening effect of gas phase method white carbon black on silicone rubber compounds is greater than that of precipitation method white carbon black.
Increasing the relative amount of reinforcing filler in the silicone rubber compound helps to improve the mechanical strength of the vulcanized silicone rubber. However, with the increase in the amount of filler, the viscosity of the liquid silicone rubber compound increases correspondingly, and the fluidity decreases. Therefore, the added amount of reinforcing filler is restricted by the fluidity requirements of the rubber compound. 3. General method to reduce the viscosity of liquid silicone rubber compound 3.1 Liquid silicone rubber base polymer To prepare low-viscosity liquid silicone rubber, using a relatively low-viscosity base polymer is the most straightforward and simple method. However, when the viscosity of the silicone polymer is too low (for example, less than 2000 mPa·s), even if reinforcing fillers are added, the obtained silicone rubber cannot achieve good mechanical properties after vulcanization, not only has low tensile strength, but also The elongation at break is extremely poor. Therefore, in order to produce low-viscosity liquid silicone rubber, the method of simply using low-viscosity polymers has certain limitations.
3.2 Filler system It is known from the production experience of silicone rubber that generally fillers with good reinforcing effect have greater thickening effect. Therefore, the viscosity of the silicone rubber compound can be adjusted by changing the ratio of the silicone rubber reinforcing filler. However, as the proportion of reinforcing fillers decreases, the mechanical strength of silicone rubber after vulcanization will also decrease significantly.
Using surface-modified silica as the reinforcing filler of silicone rubber can slow down the thickening effect of silica on the silicone rubber compound. While increasing the filling ratio of reinforcing filler and improving the mechanical properties of vulcanized rubber, the silicone rubber The increasing tendency of the rubber compound's viscosity is alleviated, so that a silicone rubber compound with better fluidity can be prepared, and the vulcanizate can also achieve higher strength. 4. Comprehensive technical measures to reduce the viscosity of liquid silicone rubber and increase the strength of vulcanized rubber 4.1 Liquid silicone rubber base polymer
⑴ Low-mole-mass polymer and high-mole-mass polymer are combined with high-viscosity base polymer to make silicone rubber with good mechanical strength, but the corresponding liquid rubber has high viscosity; conversely, silicone rubber made from low-viscosity polymer has fluidity Good, its vulcanized rubber has low mechanical strength. Based on the above rules, two polymers of the same kind with large differences in viscosity are selected and mixed in an appropriate ratio to prepare liquid silicone rubber, which will have the advantages of both and achieve better expected results: silicone rubber compound The viscosity should not be too high, and the vulcanized rubber can still achieve high mechanical strength.
⑵ The combination of short-chain base polymer and chain extender is used to prepare silicone rubber compound with relatively low viscosity. At the same time, the vulcanized rubber is required to achieve higher mechanical strength, especially silicone rubber with higher tensile elongation, such as Simply using the method of combining high and low viscosity polymers is usually still difficult to achieve satisfactory results. Only the cross-linked products of the high molar mass base polymer can achieve high elongation at break. According to this rule, the silicone polymer system is designed and the short-chain polymer and the chain extender are combined to achieve the following goals: When formulating silicone rubber compounds, polymers with low apparent viscosity are used, so the fluidity of the compounds is good; when the polymer undergoes cross-linking reaction, the chain extender will “extend” the relatively short-chain polymer, essentially The cross-linking result of the long-chain polymer is obtained, thereby obtaining a vulcanized silicone rubber with high elongation and good mechanical properties.
For example, the base polymer of two-component condensation type room temperature vulcanized silicone rubber is hydroxyl-terminated polysiloxane, and methoxy-terminated medium-low viscosity polysiloxane should be selected as the chain extender. For addition type silicone rubber, hydrogen-terminated polysiloxane should be used as a chain extender. Before the silicone rubber is not cross-linked and vulcanized, the chain extender is equivalent to the active diluent in the silicone rubber compound. Due to the presence of the chain extender, the silicone rubber compound exhibits good fluidity; during the vulcanization process of the silicone rubber, The chain extender "extends" the molecular chain of the base polymer and simultaneously crosslinks and vulcanizes to achieve the result of vulcanization with a low-viscosity rubber material equivalent to that of a high-viscosity rubber material, thereby obtaining a vulcanized silicone rubber with higher mechanical strength.
⑶ Introduce a small amount of branched polymer to improve the tear strength of vulcanized rubber. Introduce a small amount of branched polymer into the liquid silicone rubber compound. After the vulcanization of the silicone rubber, a local high crosslink density network node is formed. When the rubber is stretched and deformed, it will play the role of stress dispersion, thereby improving the tensile strength of vulcanized silicone rubber. This method is particularly effective in improving the tear resistance of vulcanized rubber. When introducing branched polymer into the rubber compound, attention should be paid to the branching degree of the branched polymer should not be too high, and its addition amount should not be too high.
4.2 Filler system ⑴ Reinforcing fillers and auxiliary fillers are used together. Reinforcing fillers are an indispensable and important component for the preparation of high-strength silicone rubber. In addition, the introduction of other auxiliary components into the silicone rubber raw materials will sometimes give the silicone rubber some additional properties. . For example, adding an appropriate amount of high-density filler to the rubber compound, although the measured viscosity value of the silicone rubber compound may increase, but it will improve the operational flow properties of the silicone rubber compound, especially for two-component liquid silicone rubber after mixing. The air bubbles in the mixed tape are very beneficial. However, it should be noted that the introduction of high-density packing may cause the disadvantages of packing sedimentation and separation. Adding an appropriate amount of anti-settling agent can slow down the packing sedimentation. ⑵ The matching of different specifications of fillers and the application of different specifications of similar fillers are also helpful to improve the performance of silicone rubber. For example, mixing precipitation method white carbon black and vapor method white carbon black can alleviate the adverse effect of the acidity of the vapor method white carbon black on the vulcanization performance of liquid silicone rubber; mix fillers with different particle sizes or different specific surface areas in an appropriate ratio , Can not only improve the fluidity of silicone rubber compound, but also improve the mechanical properties of vulcanized rubber. Silicone rubber with a proper amount of surface-modified silica as the main reinforcing filler has good fluidity. If the fumed silica without surface modification is appropriately added, it can give the silicone rubber a touch Deformability to meet the thixotropy requirements of certain specific silicone rubbers. ⑶ Filler surface modification treatment. Because of the low mechanical strength of the cross-linked product of pure organic silicon polymer, the preparation of high-strength silicone rubber must use reinforcing filler. Scientific selection and correct use of reinforcing fillers are particularly important for improving the mechanical properties of liquid silicone rubber vulcanizates. Using hexamethyldisilazane as the treatment agent, the treated white carbon black obtained by the correct treatment process is used as a reinforcing filler for liquid silicone rubber. Even if the addition amount is large, the obtained silicone rubber compound can still maintain good Of mobility. It should be noted that the treatment of silica with silazane is not as deep as possible. Generally, about 50% of the intrinsic active silyl groups on the surface of silica are replaced by trimethylsilyl groups. If the degree of surface modification of the white carbon black is too deep, although the silicone rubber compound made with this kind of white carbon black has good fluidity, the strength of the vulcanized rubber cannot reach the ideal maximum even if it is filled in a large amount.
4.3 Curing system
The cross-linking vulcanization aid of liquid silicone rubber is not only related to the cross-linking vulcanization speed of silicone rubber, but also related to many properties of vulcanized silicone rubber. ⑴ The ratio of crosslinking agent to base polymer In each component of liquid silicone rubber, the main function of the crosslinking agent is to carry out crosslinking reaction with the base polymer to realize the vulcanization of silicone rubber. In the two-component condensation reaction vulcanized silicone rubber, when the silicate crosslinking agent is used in excess (the molar ratio of the base polymer is tens or even thousands of times), although it can accelerate the vulcanization speed of the rubber compound, The shrinkage rate of silicone rubber during vulcanization is large, and the vulcanized rubber will gradually become hard and brittle with the extension of time, and the tear strength will drop sharply. The crosslinking agent in one-component condensation type room temperature vulcanized silicone rubber actually assumes multiple functions such as crosslinking agent, moisture scavenger, stabilizer, etc. A proper excess of crosslinking agent is necessary, but a large excess of crosslinking agent is required. It will obviously delay the vulcanization speed of silicone rubber, and there are also disadvantages of large shrinkage rate of silicone rubber after vulcanization and gradual hardening and brittleness. According to the molar mass of the base polymer and the total content in the rubber compound, the amount of crosslinking agent is adjusted according to the ratio of the smooth crosslinking and vulcanization of the silicone rubber to ensure that the silicone rubber achieves the best mechanical strength. ⑵ Catalysts, accelerators, inhibitors and vulcanization reaction speed control most applications of liquid silicone rubber require an appropriately fast vulcanization speed. The use of catalysts can accelerate the cross-linking reaction. For the liquid silicone rubber used for coating and potting, a catalyst or accelerator that moderates the start-up speed of the vulcanization reaction and accelerates the post-curing reaction appropriately. The liquid silicone rubber compound used for mass construction requires an inhibitor to prolong its bath life or operating time. The condensation reaction vulcanization type liquid silicone rubber generally uses metal organic acid salts such as dibutyltin dilaurate as a catalyst. Because the organotin catalyst plays the role of catalytic crosslinking, it also has the effect of reverse catalytic degradation and reversion. Excessive amount of catalyst will greatly reduce the heat resistance of vulcanized silicone rubber, so the amount of organotin catalyst should not be too large . For silicone rubber that requires rapid vulcanization, vulcanization reaction accelerators, such as titanate chelate, should be introduced to further accelerate the vulcanization reaction. The most suitable catalyst for the crosslinking reaction of addition type silicone rubber is platinum-methylvinylsiloxane complex. The prepared platinum catalyst is not as active as possible. The highly efficient platinum catalyst is more sensitive to the poisons that affect the hydrosilylation reaction. The extremely sensitive catalyst has a small amount in the silicone rubber. It is easy to encounter in individual application environments. Poisoned and invalidated. A stable catalyst can ensure the complete vulcanization of the silicone rubber and make the vulcanized silicone rubber achieve the best use effect. ⑶ Condensation reaction vulcanization type silicone rubber vulcanizing agent packaging For two-component condensation type room temperature vulcanization silicone rubber components, appropriately reducing the amount of crosslinking agent can slow down the tendency of vulcanized rubber to continue to harden and become brittle after vulcanization, but the proportion is too low The amount of vulcanizing agent may not be conducive to the precise proportioning operation of the on-site compounding compound. For this, low-viscosity methyl silicone oil or methoxy-terminated silicone oil can be used as a diluent. It should be noted that: general methyl silicone oils more or less contain hydroxyl-terminated silicone polymers. This part of silicone-based hydroxyl-containing silicone polymers must undergo condensation reaction with the crosslinking agent when coexisting with the vulcanizing agent component. , Resulting in a sharp increase in the viscosity of the vulcanizing agent or even gel, or loss of vulcanization function. Therefore, if methyl silicone oil is used as a diluent, it must be treated in advance to remove silanol. Most two-component room temperature vulcanized silicone rubbers are packaged in separate packages of silicone rubber compound and vulcanizing agent. It should be noted that because general plastic materials have gas permeability, including moisture permeability, this may cause crosslinking agents and catalysts to be hydrolyzed and invalidated by moisture. In addition, most of the thermally stabilized additives in plastics have a toxic effect on the catalysts of addition molding silicone rubber. Therefore, do not use polyethylene, polyvinyl chloride and other general plastic containers to package the silicone rubber vulcanizing agent components.
4.4 Mixing process and compounding technology (1) Kneading and mixing of silicone rubber compound The production of liquid silicone rubber mostly undergoes the kneading and mixing process of silicone polymer and filler. The kneading and mixing operation is not only the simple mixing of materials, but the extrusion and shearing of the materials during the kneading process actually promotes the infiltration of the filler and the polymer, and the filler is uniformly dispersed in the polymer to play a reinforcing effect. During the kneading process, the high-consistency material has strong shearing effect and high mixing efficiency. For the mixture of low filler ratio system (relatively thinner viscosity), the extrusion resistance cannot be formed when it is stirred by the stirring blade of the kneader, that is, the material with too low viscosity Failure to withstand effective kneading and shearing will affect the reinforcement effect. Therefore, even if the silicone rubber material with low filling ratio is produced, it is best to undergo kneading of high viscosity thick material first, and then add polymer to dilute it to a predetermined low filling ratio. ⑵ For the processing of the silicone rubber compound, directly use the paste obtained by kneading at room temperature to prepare the silicone rubber compound. The fluidity of the silicone rubber may not be good. The paste should be properly heat-treated. The low molecular weight in the compound It is equivalent to a modified treatment agent, which can improve the infiltration of the polymer and filler surface, while reducing the viscosity of the rubber and improving the mechanical properties of the vulcanizate. It is not advisable to use a high-speed mixer to produce liquid silicone rubber with long-term high-speed shear. Because the silicone polymer undergoes high-speed shearing for a long time, part of the silicone polymer chain may be sheared. Although the viscosity of the obtained silicone rubber is thin, the mechanical properties of the vulcanized rubber will be significantly reduced. In the same way, when the liquid silicone rubber passes through the three-roll mill, it is necessary to control the appropriate roller distance to ensure the shearing and kneading effect, and at the same time to prevent the silicone polymer chain from being cut. 5. Summary In order to develop and produce liquid silicone rubber with low rubber viscosity and good mechanical strength of the vulcanized rubber, it is impossible to achieve the desired goal by simply using a low molar mass base polymer and increasing the proportion of fillers. According to the specific requirements of liquid silicone rubber's process performance and use performance, comprehensive use of basic polymer combination, appropriate filler matching and vulcanization system, with fine mixing